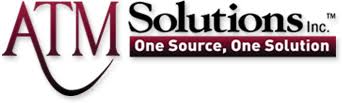
Introduction
To provide administrative support by picking stock to be issued to the local technicians and the regions, receiving stock from suppliers and the repair centre, packing stock in the allocated areas, updating stock bins and carrying out weekly and monthly stock take to ensure that stock is received by parties that request it and to avoid shrinkage.
Duties & Responsibilities
Picking
- Obtaining a requisition on the Astute system and pulling stock according to the requisition for the regions and local stock requests
- Updating the bin card on the Astute system and on the physical shelf if stock is taken, to ensure that the stock is accurate
- Putting stock that has been drawn in a designated area and requesting another stores employee to verify that the stock is correct
- Packing the checked stock in box so that it can be couriered
- Writing waybills for items for be couriered and ensuring that the box size and weight are correct
- Updating the waybill number on the Astute system in order to generate an order confirmation, which is automatically sent to the person who requests the stock
- Making sure that parcels are ready in time for the courier company’s daily collection
Receiving
- Receiving stock from suppliers and obtaining the paperwork for each delivery
- Arranging for the forklift driver to offload palettes
- Checking the offloaded stock against delivery note to ensure that the delivery note from the supplier agrees with the internally generated Purchase Order
- Checking the quantity of stock delivered
- Writing down the quantity of stock on their delivery note, signing the paperwork, keeping one copy of the delivery note and returning a copy of the delivery note to the person making the delivery
- Completing details of stock received, including the number of parcels received, in the receiving book and ensuring that the person making the delivery signs the necessary paperwork
- Packing stock that is received onto shelves at the end of each day and updating the bin information
- Taking supplier delivery notes and documentation to the inventory specialist to sign off and then to the financial manager in operations to update
Packing
- Putting stock on the assigned racks when it is received from suppliers or the QA Department
- Writing the dates that stock was received and the quantity of stock received on the bin card
Stock Take
- Conducting weekly stock takes on Mondays to identify the status of the “fast movers” stock
- Obtaining a list from the inventory specialist that details the critical stock and the items on back order
- Identifying stock items where the quantities are less than the minimum required and bringing them to the attention of the inventory specialist and the stock replenishment officer to identify whether orders should be placed for the items
- Conducting monthly stock takes with all stores staff by obtaining a list from the inventory specialist that details the critical stock and the items on back order
- Tracking back orders, which occur when the request for stock exceeds the amount available in stock and writing the information on a manual back order form and sending it to the repair centre manager/supervisor
- Sending backorder requests to the repair centre by Wednesday or Friday each week.
- Providing feedback to the regions, explaining when there is a stock shortage and advising them to reorder the stock with the next weeks’ order
Desired Experience & Qualification
- Matric
- Any Warehousing Course would be an advantage
- 1-2 years’ experience in picking and packing
- MS Office
- Astute will be an advantage
- Knowledge of ATM parts will be an advantage
- Must have a valid forklift license
Package & Remuneration
CTC
Leave a Reply